Daniel R. Lewin
Personal Info
D.Sc. 1984, Technion-Israel Institute of TechnologyResearch Fields
Processes, Sustainability: Environment, Water, and EnergyResearch Topics
FC – Model-based Control of Fuel Cells
In the past few years, fuel cells have generated much interest as an alternative to fossil fuels as an energy source. The dynamic response of fuel cells is important for vehicular applications, since the power demands fluctuate, and thus the optimal steady-state operation conditions do not exist. Thus, the relevant issue is how to control the fuel cell to ensure acceptable response time for the power demand, while at the same time maximizing its fuel efficiency. To address this problem, a dynamic fuel cell model has been developed taking into account spatial dependencies of voltage, current, material flows, and temperatures. This model, together with dynamic models of a fuel reformer and heat exchanger, has been used to examine dynamic characteristics of an entire fuel cell system. A model-based control scheme, based on a reduced model is under development, which treats the system as a whole, optimizing the overall performance over time.
WFCM – Yield Enhancement in Photolithography using Model-based Control
The manufacture of integrated circuits involves the formation of microscopic features on silicon wafers, which give them their desired electronic characteristics. These features are formed using photolithography, in which the features are printed onto the surface of the circuit, and it is important to ensure that they are reproduced repeatedly and accurately. We have developed a model-based controller, based on their unique genetic programming technology, that can ensure repeatable line widths (referred to as critical dimension or CD) in photolithography. The work has involved the modeling of a critical processing step at Tower, and their use of the model as a test-bed and for control design. Within six months of beginning work with Tower, the controller operated successfully at its first trial.
The initial results show that overall process yields have increased as a result of using the controller on-line. The chart on the right shows FAB results indicating excellent disturbance-rejection in dense and isolated CD using the stepper dose and focus, as well as marked increases in yield (in the bottom plot) significantly higher than the accepted values at Tower (indicated by the dotted line). The controller is currently being extended to compensate to the observe variability observed from field-to-field.
Yield Enhancement in Bioprocessing by Integrated Design and Control
Controlling bioprocesses at their optimal states is of considerable interest to the pharmaceutical industry since it enables the reduction of production costs and the increase of yields while at the same time maintaining quality. As estimated by the Food and Drug Administration (FDA), poor quality design is responsible for more than 40% of product recalls. The design of control for bioprocesses is not straightforward due to the following reasons: (a) they are characterized by significant model uncertainty, (b) they are time varying and nonlinear, (c) there is a marked lack of reliable on-line sensors, and (d) the typical response time is extremely slow. Numerous solutions can be found in the literature that attempt to overcome these difficulties. This research will focus on identifying and developing a novel approach to enhance the yield of bioprocesses, specifically in the pharmaceutical industry, using Six-Sigma methodology as a tool to find bottlenecks and overcome them. The modeling of the process will be accomplished in two ways: (a) Steady-state modeling of the process will be carried out using a commercial package. (b) Dynamic process models will be created by means of first principles modeling based on physical knowledge and will be calibrated using real data from a leading pharmaceutical manufacture. These models, together with Six-Sigma methodology, will allow process improvement by introducing new control strategies and/or modification to the process design. The improvements will increase the sigma-level of the entire process, which is identical to increasing process yield. The new novel approach, which combines Six-Sigma methodology together with modeling and integrated design and control, will improve process yield to ultimately speed-up production time. This can make a difference in the pharmaceutical industry in terms of product quality, investment and time. A process that will show high sigma-levels will receive faster approval by the FDA, which translates directly to a faster return on investment. To make this research more realistic, collaboration with a leading pharmaceutical manufacturer is needed.
Publications
W. D. Seider, J. D. Seader D. R. Lewin and S. Widagdo, Product and Process Design Principles: Synthesis, Analysis and Evaluation, John Wiley and Sons, New Jersey (2009).
J. Golbert and D. R. Lewin, “Model-based Control of Fuel Cells: (2) Optimal Efficiency,” Journal of Power Sources, 173(1), 298-309 (2007).
E. Dassau, I. Zadok and D. R. Lewin, “Combining Six-Sigma with Integrated Design and Control for Yield Enhancement in Bioprocessing,” 45(25), 8299-8309 (2006) .
J. Golbert and D. R. Lewin, “Model-based Control of Fuel Cells: (1) Regulatory Control,” Journal of Power Sources, 135(1-2), 135-151 (2004) .
B. Grosman and D. R. Lewin, Automated Nonlinear Model Predictive Control using Genetic Programming,” Comput. Chem. Eng., 26(4-5), 631-640 (2002).
S. Lachman-Shalem, B. Grosman and D. R. Lewin, Nonlinear Modeling and Multivariable Control of Photolithography, IEEE Trans. of Semiconductor Manuf., 15(3), 310-322 (2002).
G. E. Rotstein and D. R. Lewin, “Simple PI and PID Tuning for Open Loop Unstable Systems”, I. & E. C. Res., 30, 1864-1869 (1991).
Daniel R. Lewin
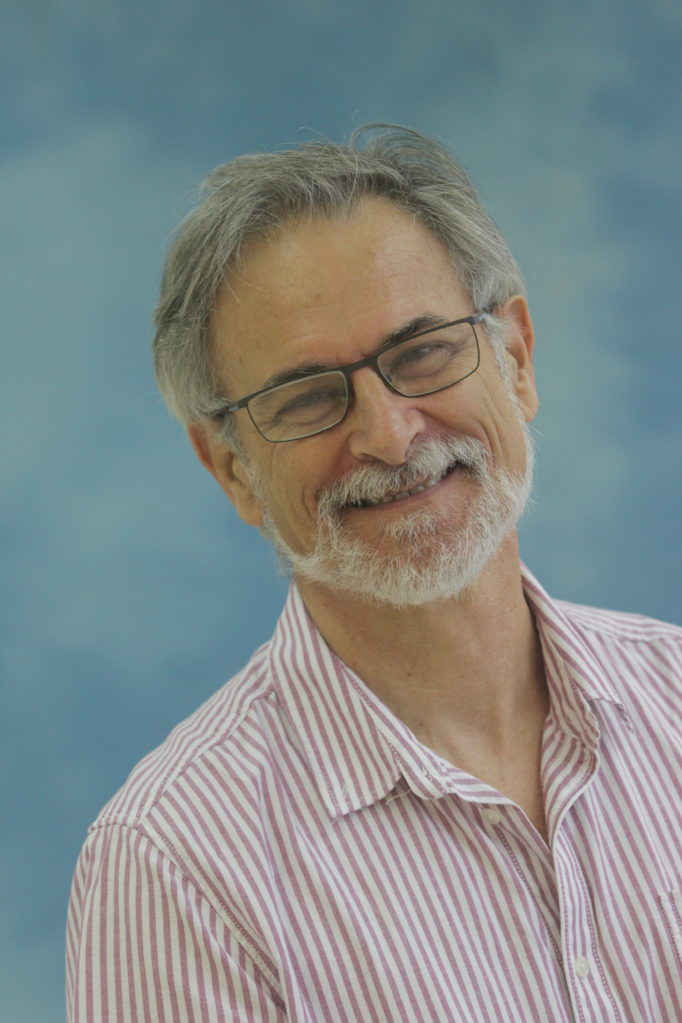